In the previous part of this series we examined which was the best O-ring material for use in high temperature applications (over 150°C). Today, we will explore what is the best low temperature O-ring according to several working demands. For the most part, many compounds already support a sub degree service temperature ranging from -5 to -25°C, for this reason we will only examine low temperature applications under -25°C.
For working conditions below -25°C, you may wish to consider the following materials; NBR LT, HNBR LT, VMQ, FVMQ, Kalrez® 0040, Polymax P045B7LT, FEP Encapsulated O-rings and Astra seals.
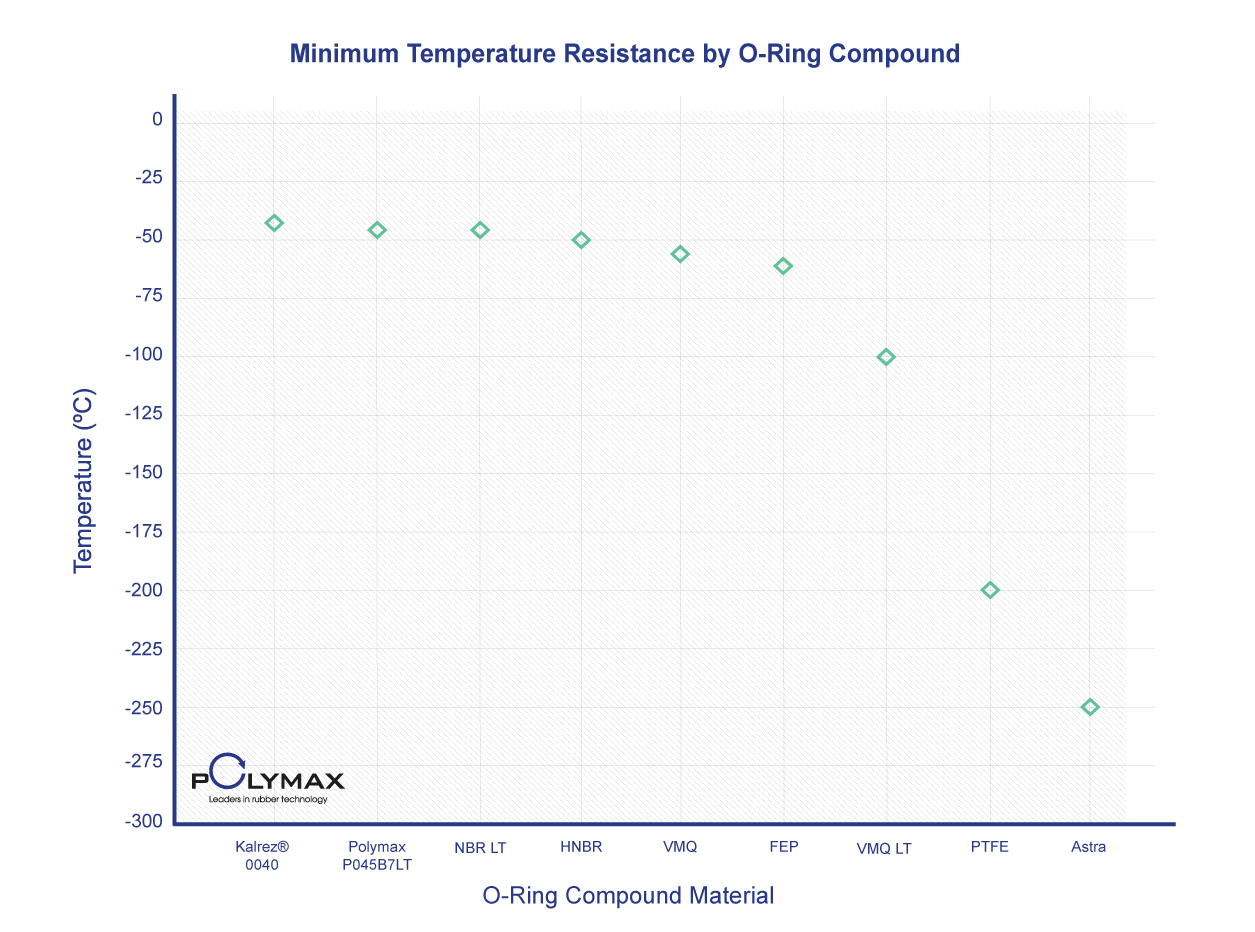
What causes O-ring failure at low temperatures?
The effect of cooling causes rubber to lose its elasticity, which is measured as the ‘Compression Set’ of the elastomer. The compression set is an integral part of O-ring performance necessary to provide a reliable seal, defined as the percentage of the material that fails to return to its original size after compression. Therefore, a lower compression set indicates a better resistance to changes in pressure (dynamic) and continuous strain (static) whilst providing the required ‘seal line’ between the O-ring and seal casing. The worsening of compression set in low temperatures leads to seal leakage and ultimate O-ring failure.
To counteract the loss in compression set, the seal casing can be designed with a continuous pressure on the O-ring, called the ‘squeeze’. Setting a squeeze of 30% or higher may prevent the O-ring from failing in cold temperatures but this has its limitations. For instance, it’s not practical to use a squeeze above 16% in dynamic applications due to friction and wear.
Glass Transition in Rubber Materials
Subjecting the O-ring to further low temperature extremes causes the material to enter what is known as ‘The Glass Transition’ or ‘Tg’. This is where the polymer reaches a temperature where it becomes hard and brittle, known as it’s ‘glassy state’. Materials are tested under ASTM D7426 or ISO 22768 to determine the Tg temperature. In terms of low temperature elastomers, reaching the glass transition could cause the O-ring to crack or shatter.
An interesting point about the glass transition is that certain materials such as hard plastics can have a Tg above room temperature. For example, polyisoprene has a Tg above 100°C and that is why it behaves differently to other polymers. To find out more about glass transition, this web page offers a more comprehensive explanation.
TR-10 Temperature Test
Finally, the most reliable test used to determine the minimum functional temperature of the O-ring is the TR-10 test. Carried out under both test standards ASTM D1329 and ISO 2921. It involves cooling the material to gradually lower temperatures and stretching the compound by 50%. The lowest temperature reached before failure determines the minimum working temperature of the O-ring.
What is the Best Low Temperature O-ring?
To begin with, its important to realise that the majority of elastomers have alternative formulas that may lower the working temperature of the compound. For situations where a particular material has proven suitable due to its chemical compatibility or mechanical properties there may be a low temperature (LT) version available.
Low Temperature Nitrile O-ring
Temperature Range: -45°C to 110°C
Nitrile LT Pros: Low cost, moderate oil, chemical and grease resistance.
Nitrile LT Cons: At low temperatures, prone to shrinking and can lose chemical resistance.
In this example, formulating nitrile with lesser amounts of acrylonitrile improves its low temperature resistance. Unfortunately, it also affects the elastomers fuel and oil resistance. Nitrile LT is a great choice for low cost sealing that requires moderate to little chemical exposure.
Low Temperature HNBR O-Ring - Datasheet
Temperature Range: -50°C to +150°C
HNBR LT Pros: Improved chemical and oil resistance.
HNBR LT Cons: At low temperatures, prone to shrinking and can lose chemical resistance.
In comparison to nitrile, changing the acrylonitrile content in the hydrogenated version of nitrile (HNBR) results in a loss of flexibility, read this report for more information. HNBR provides superior mechanical properties in comparison with NBR which helps prevent extrusion and wear. It is also resistant to a wider range of oils, fuels and chemicals. Most notably, aliphatic hydrocarbons, hydraulic fluids and dilute acids. Whilst not recommended for use with chlorinated hydrocarbons, polar solvents or strong acids.
Low Temperature Silicone O-ring
Standard Temperature Range: -55°C to +200°C
Fluorinated Temperature Range: -60°C to +200°C
Special LT Compound Temperature: -100°C to +220°C
Silicone Pros: Outstanding low temperature resistance.
Silicone Cons: Poor wear resistance and little chemical compatibility.
Demonstrating impressive performance at both extremely high and low temperatures, silicone has a working service temperature down to -55°C, with specially compounded versions capable of -100°C. Comparatively, that is 50°C lower than the majority of standard O-ring materials. However, the drawback is silicone's poor tear strength and wear resistance making it unsuitable for dynamic applications.
As for chemical compatibility, silicone is resistant to animal and vegetable oils but is vulnerable to most acids and alkalis, hydrocarbon based fuels and petroleum based oils. Due to this, the fluorinated version of the compound Fluorosilicone (FVMQ) may be considered but is still limited against contact with ketones, phosphate ethers, some acids, brake fluids and amines. FVMQ offers a working temperature down to -60°C.
Kalrez® 0040 - Datasheet
Temperature Range: -42°C to +220°C
Kalrez Pros: Great all round chemical resistance.
Kalrez Cons: Expensive solution.
The most commonly sought after elastomeric material for use with aggressive chemicals is FFKM. The well known sealing brand DuPont™ offer a Kalrez® perfluoroelastomer designed to provide the best sealing performance under extreme low temperature working conditions. Kalrez® Spectrum™ 0040 is an excellent choice in applications for applications due to its great chemical resistance and elasticity.
Polymax FFKM P045B7LT - Datasheet
Temperature Range: -45°C to +240°C
P045B7LT Pros: Great all round chemical resistance, less expensive than Kalrez®.
P045B7LT Cons: More expensive in comparison to general compounds.
Conversely, alternative FFKM brands can provide a comparative level of performance at an economical price. For instance, Polymax P045 provides reliable sealing performance at -45°C and is resistant to an almost universal spectrum of chemicals. Making it suitable for use within the petrochemical, food processing and pharmaceutical sectors.
PTFE O-rings
Temperature Range: -200°C to +250°C
PTFE Pros: Outstanding low temperature and chemical resistance.
PTFE Cons: Poor compression set, little to no memory.
For instances where compression set is not an important factor, PTFE provides outstanding cold temperature resistance down to -200°C and is unaffected by virtually all known acids, alkalis and solvents. Another benefit of PTFE is the material has a low coefficient to friction, meaning its surface is very slippery and it won’t require lubrication at assembly. Whilst the material is very tough and abrasion resistant, PTFE has little to no compression set, hence it dents easily and may not provide a reliable seal if put under continuous pressure.
FEP Encapsulated O-rings
Encapsulated Silicone Temperature Range: -60°C to +204°C
FEP Pros: The elastomer can suit different working conditions.
FEP Cons: Expensive solution.
Making the most of PTFE's outstanding chemical resistance, the material is utilised as a protective casing over a standard O-ring. In this example, selecting silicone as the inner O-ring consequently offers a working low temperature range down to -60°C. Adaptable to many environmental demands, the FEP encapsulated O-ring can be interchanged with materials suitable for FDA, USP CLASS VI, metal detectable and semi conductive applications.
Astra seals
Temperature Range: -250°C to +204°C
Astra Pros: The best low temperature compression set, no Tg state.
Astra Cons: Only recommended for axial sealing applications with no stretch.
Finally, the best solution for resistance to extreme cold temperatures is an O-ring that doesn’t contain any rubber at all. Astra seals combine a 302 stainless steel ribbon with a FEP encapsulated O-ring casing. In effect creating an O-ring that is capable of sub temperatures down to -250°C whilst sustaining an outstanding compression set and universal chemical compatibility. Consequently, this type of O-ring is now the preferred choice for space shuttle rockets and other astronomical applications.
We write articles about rubber chemistry to make life easier for engineering professionals. Sign up to our mailing list for bi-monthly content straight from the rubber press.